For Overseas Business
On-Site Type N-Methyl-2-Pyrrolidone (NMP) Solvent Recovery and Purification System
This on-site facility recovers the NMP gas generated in the manufacturing processes for lithium-ion secondary batteries for purification into a high-purity NMP solvent.
Conventional NMP Recovery and Purification Process
In the conventional process, the raw materials are resolved with the NMP solvent, treated with a coater, and dried. The generated NMP gas is then recovered and transported to a purifying contractor with a tank truck. The purified NMP solvent is returned to the production site by the tank truck and reused as a solvent for the raw material.
Issues of Conventional Process
- The running cost is high because of the loss of the NMP solvent, the transport cost by tank truck, and the purification cost by the contractor.
- The VOC gas is exhausted into the air from the recovery unit.
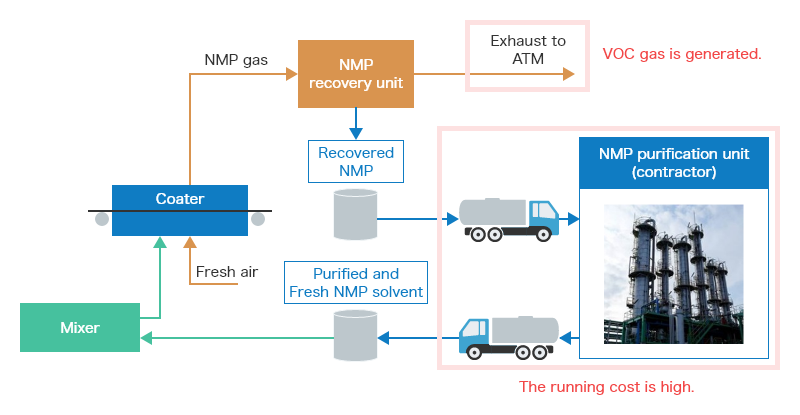
On-Site Type NMP Recovery and Purification Process
The outdoor exhaust generated from the NMP recovery unit is reused, and the recovered NMP solvent transported to the contractor by tank truck is refined at the production site. The self-contained, on-site NMP recovery and purification process reduces transportation costs and increases the high quality of the recycled NMP solvent.
Advantages of Our Process
- By installing the purification facility on the production site, high-quality NMP solvent can be consistently available for use. The NMP solvent is recovered, purified, and transported within a closed system, which prevents the contamination caused by the loading and unloading of the solvent onto/from the tank truck and which, as a result, also prevents environmental pollution from leaks and diffusion.
- The process reduces the costs of transport by tank truck and purification by the contractor.
- This also reduces the emission of the VOC gas.
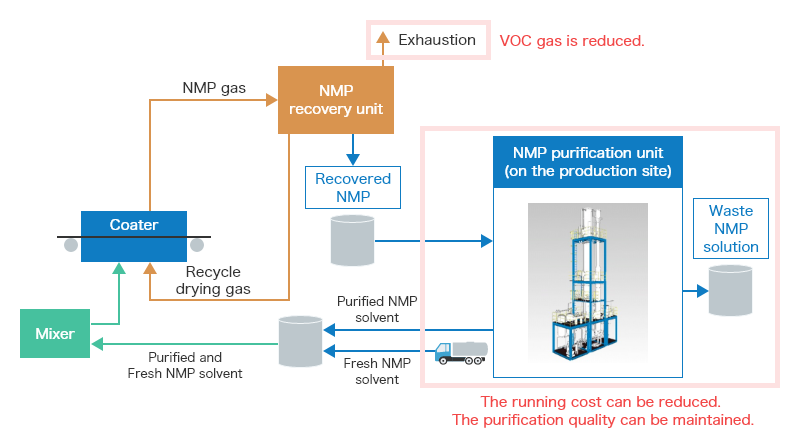
Features of NMP Recovery and Purification System
- Achievements and Trust
- We have delivered over 40 units to Europe, the United States and Southeast Asia.
- High Performance
- High recovery rate (95%) and high-quality purification (99.9 wt%) - > The solvent can be purified and reused at the production site, which reduces costs.
- Usability
- By pressing a button, the facility operates automatically. -> A plant can operate stably even if the operator lacks experience in operating a chemical plant.
- Cost Reduction
- The cost of utilties can be reduced.
- Space Saving
- The adoption of the skid structure reduces the installation space and on-site construction period.
Construction of Plant in Taiwan – Total Engineering Services
By establishing the project office, we can undertake construction projects and offer engineering services from procurement to construction (EPC). The construction projects are supported by our affiliate in Taiwan, Ling-Young International Engineering Corporation.
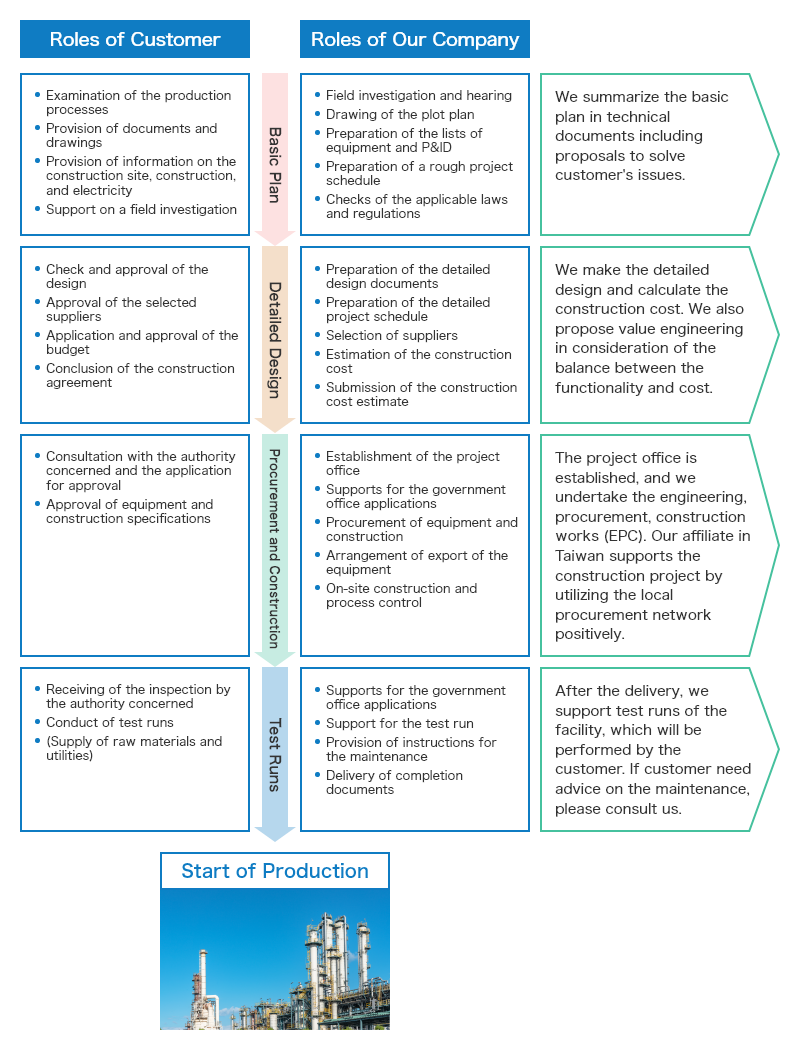
Modular Construction Method
When a plant is constructed abroad, numerous equipment, pipes, ducts, and frame structures are generally installed in the order of foundation work, installation, and assembly. With our modular construction method, modules are assembled at the factory and then disassembled and packed for transport to the construction site. The modules are then reassembled at the construction site.
Advantages of Modular Construction Method
- By manufacturing at a plant with high cleanliness, the modules can be used for facilities that use solvents for semiconductors and electronic devices that should avoid contamination. Since the modules are manufactured in the clean booth of the factory, the quality of the modules is improved.
- At the construction site, the facility is constructed mainly by assembling the modules so that the construction period and cost can be reduced.
Related Technologies and Services
-
Solvent Recovery Technology (Recovery and Purification)
The organic solvents (such as NMP, DMF, and DMAc) used in manufacturing plants are recycled through a fully automatic facility using environment-friendly, energy-saving technology.
-
Cyclone Scrubber
Proposal for Reduction of Noise and Environmental Load and Polymer Collection System
-
Modular Construction Method
Stabilization of Quality of Production Equipment and Reduction of On-Site Construction Period
-
MECTRNR®: Operator Training System
-
Film Casting Machine
Steel Belt Film Casting Machine Optimal for the Film Forming Process of the Dissolution Flow Casting Method