Semiconductors, Batteries, and Electronic devices
Since 1983, we marketed the necessary chemical solution supply and recovery systems for the manufacturing processes of semiconductors, batteries, and electronic devices. Over 2,000 systems have been delivered to our customers. As a pioneer in chemical solution supply and recovery systems, the highest priority is to quality and safety; therefore, we offer solutions that can be used safely.
1Core Technologies for Chemical Solution Supply Systems for Manufacturing Semiconductors, Batteries, and Electronic Devices
In order to meet the different applications of semiconductors, batteries, and electronic devices that have evolved so rapidly, we propose optimal solutions for the manufacture of raw materials and the supply, recovery, recycling, and reuse of chemical solutions through the use of a wide range of technologies accumulated in the chemical and electronics fields. We also contribute to the attainment of the customers’ environment, social, and governance (ESG) goals, sustainable development goals (SDGs), and the goals for achieving energy savings and carbon neutrality.
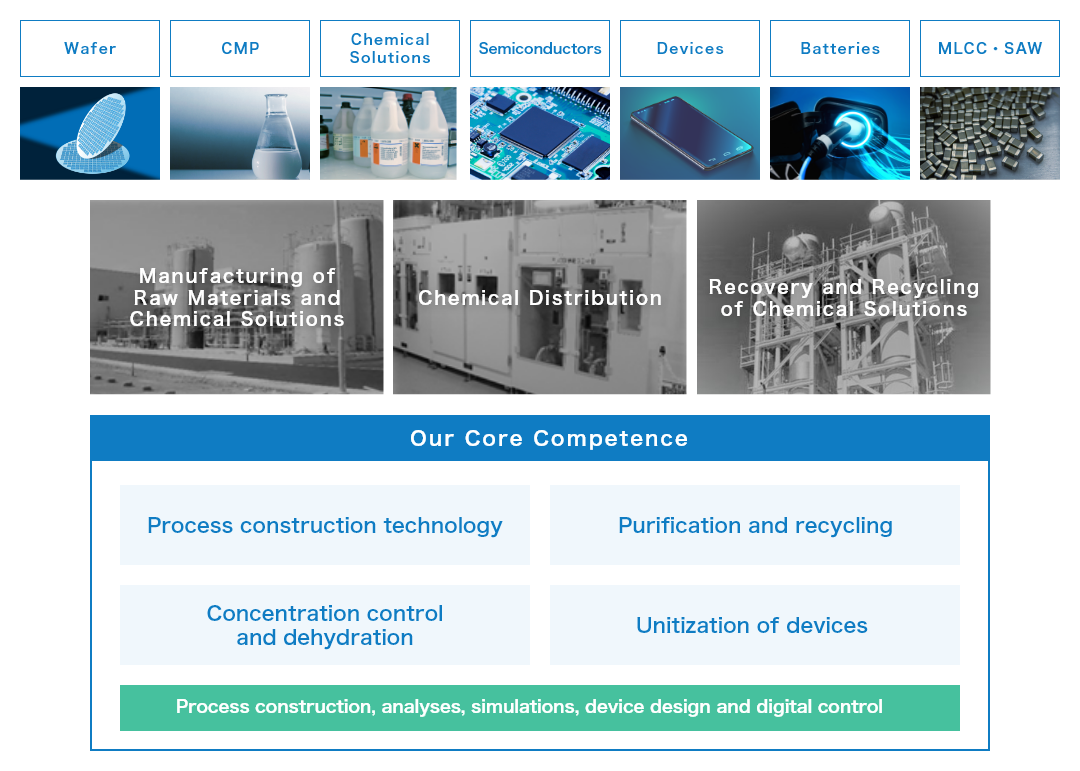
2Lineup of Chemical Solution Supply, Recovery, Purification, and Concentration Control Systems
As a leader in chemical solution supply systems, we help to ensure manufacturing quality and reductions in the manufacturing costs and the environmental load by providing systems that support ultra-fragmentation and qualitative improvements in the manufacturing process through the use of chemicals. The applicable fields include the manufacturing process for batteries, as well as the products and materials used in electronic devices, which have remarkably expanded their markets. We propose optimal solutions to many more extensive fields.
- Chemical Distribution System
Chemical Distribution System
CDS: Chemical Distribution System
We make effective use of the know-how developed at Mitsubishi Chemical Corporation, our corporate group and chemical manufacturing branch, to safely provide systems that distribute chemicals to their respective use points while also maintaining maximum quality.
Features
- Economical and space-saving
- Our systems are designed to provide optimal cost, and fit into a compact space, after understanding the properties of chemicals well.
- Reduced environmental impact
- Our Chemical Distribution Systems are designed with recycling in mind, and reduce both the amount of chemicals consumed and amount of waste generated.
- Scheme building
- We provide schemes that go beyond the system itself to even include consideration of waste collection destinations.
Applications
Our Chemical Distribution System is especially useful in semiconductor, LCD panel, solar panel, and lithium battery manufacturing facilities.
Specifications
We offer distribution systems tailored to match the amount of chemical use of each customer.
Small Consumption distribution: Transfer from drums
Large consumption distribution : Transfer from lorry
- Economical and space-saving
- Slurry Distribution System
Slurry Distribution System
SDS: Slurry Distribution System
Our Slurry Distribution System makes it possible to distribute slurry from a single distribution unit to multiple use points while maintaining consistent physical properties of the slurry to be used in polishing processes.
Equipment overview
The equipment in our Slurry Distribution System provides the polishing slurry used in chemical mechanical polishing of crystal surfaces used in such applications as semiconductors and solar cell substrates.
Features
- Accommodates a wide range of slurries (e.g. Silica-based, cerium-based, alumina-based)
- Employs physical properties and parts (e.g. tank, pump, valve) that take into account the physical properties of slurry
- Polishing processes are made consistent due to periodic cleaning performed by its automatic cleaning system
- Economical and space-saving
- Designed to provide optimal cost and fit into a compact space after understanding the properties of chemicals well.
- Able to accommodate large containers
- Has a proven track record of use in many 300 ㎜ processes
Applications
Our Slurry Distribution System is useful for semiconductor related production equipment.
Specifications
- DRS: Developer Recycling System
DRS: Developer Recycling System
DRS: Developer Recycling System
Equipment overview
Our Developer Recycling System performs appropriately-timed control of concentrations for TMAH (Tetra-Methyl Ammonium Hydroxide) and other chemicals used in developing process of LCD panels and other products. Doing this makes it possible to reduce developer consumption while also ensuring a stable developing rate.
Features
- Manages the real developer concentrations (that contain no carbonate), as well as the concentrations of photoresist and carbonate
- Makes it possible to uniformly control the developing rate (critical dimension)
- Monitors developing components in real time by using a multi concentration analyzer
- Dramatically reduces the consumption of TMAH and dilution water (ultrapure water) by its ability to achieve a 100% recycle rate of waste liquid
Applications
Our system is used to manage concentrations of TMAH, resist, and carbonate, which are used in the developing process of LCD panels and other products.
Specifications
Schematic diagram
- Developer Dilution System
Developer Dilution System
DDS: Developer Dilution System
Our system dilutes the developer used in the process of semiconductors and LCD panel production. Dilution is performed right at the customer's plant with extremely high accuracy by using the "step by step method." Our system makes it possible to realize significant cost savings compared with purchasing pre-diluted developer.
Features
- Proposed a concentration analysis unit that will fit best with the customer's needs
- Guaranteed dilution adjustment with an accuracy of ±0.002wt% or less (actual results show ±0.001wt% or less)
- Using jet agitation to reduce mixing time
- Proven results in state-of-the-art semiconductor plants
Applications
Our Developer Dilution System is useful in semiconductor related manufacturing facilities and LCD panel related manufacturing facilities.
Specifications
- Photo Resist Distribution System
Photo Resist Distribution System
PRDS: Photo Resist Distribution System
Our system can utilize large-sized containers and deliver consistent photo resist distribution without bubbles, for liquid crystal panel manufacturing processes.
Features
- Reduces chemical cost as well as the frequency that containers need to be changed, which is accomplished by taking advantage of large-sized returnable containers
- Central distribution is performed by using 200 L and 1000 L containers
- Able to distribute photo resist without bubbles
Applications
Liquid crystal panel manufacturing equipment
Specifications
- High purity purification system
High purity purification system
HPPS: High purity purification system
Overview
This system purifies chemical solution used for the production process of the next-generation semiconductors by distillation and provides ultra-purity chemicals whose metal concentration is reduced at the level of single digit value in ppt.
Features
- Metal concentration at the level of single digit value in ppt
- Full-automatic operation
- Skid type saving the space
- Organic Solvent Dehydration System
Organic Solvent Dehydration System
OSDS: Organic Solvent Dehydration System
Our system dehydrates and purifies organic solvents by using a zeolite pervaporation membrane. The system can be used in a wide array of applications, such as reforming organic solvents with unstable quality into electronics-grade.
Equipment overview
The equipment uses a zeolite pervaporation membrane to selectively remove water contained in organic solvents.
By using the MSM-1 membrane developed by our group company Mitsubishi Chemical Corporation, we have made it possible to reliably process acidic organic solvents that could not be handled with conventional zeolite membranes and organic solvents with high ratios of water content.Our system also makes it possible to remove impurities by adding an eon removal unit or evaporation unit to it.
left: IPA recovery purification system (S111), right: Membrane module
Features
- System is very compact and fully utilizes the capabilities of its pervaporation membrane (can be unitized)
- Uses a highly durable ceramic membrane that has superior heat, water, and acid resistance
- Able to highly refine organic solvents
- Utility requirements are primarily just a power source and cooling water (steam not Required)
- Employs a highly reliable and safe system that is representative of our many years of successful installations
- A wide range of systems are possible from manual to fully automatic
Applications
Our Organic Solvent Dehydration System is useful in solvent recycling, reducing waste liquid, and other applications.
Equipment delivered experience
Ethanol dehydration system
IPA dehydration and purification system
Operating principal: pervaporation method
Major compatible solvents
Isopropyl alcohol (IPA), ethanol, acetone, N-Methyl-2-pyrrolidone (NMP), acetonitol, ethyl acetate, butyl acetate, toluene, THF, DMF, DMSO, MEK, etc.
- NMP Purification System
NMP Purification System
NRS: NMP Refining System
Our system recycles NMP recovered from the lithium-ion secondary battery manufacturing process into highly pure NMP by using fully automated on-site refining equipment. It is patented in Japan and China.
Features
- Compatible with all NMP recovery methods (absorption, adsorption, condensation)
- Refines NMP to a purity of 99.9wt% or higher
- Extremely low operating cost (UTT, etc.)
- Comes in a space-saving "skid" type
- Fully automatic operation
Flexible processing capability design
We will also design and build types not shown in the right diagram to meet your processing capacity requirements.
Applications
Our NMP Purification System is useful in lithium ion secondary battery manufacturing facilities.
Schematic drawing
- On-site Mixing System
On-site Mixing System
OMS: On-site Mixing System
Our On-site Mixing System mixes multiple chemicals used in manufacturing right at the customer's worksite. It comes equipped with a high-precision inline concentration measuring device for controlling chemical concentrations with high accuracy.
Equipment examples
-
1Mixing 2 or 3 single acids.(Equipment delivery experience)
- Al etchant solution: H3PO 4 + HNO 3 + CH3COOH
- Si etchant solution: HNO 3 HNO 3, + HF + HF+CH3COOH
-
2Diluting and mixing powder or high-concentration liquid.(Equipment delivery experiences)
- ITO etchant solution: (COOH)2 powder
- Photo resist (color filter): Na2CO3 powder
- Stripper (color filter): KOH powder
Features
- System comes equipped with a high-precision inline concentration measuring device
- Contributes to reducing logistics costs
Applications
Our On-site Mixing System is useful in LCD panel production related facilities and semiconductor related manufacturing facilities.
Specifications
Shown below is a schematic diagram of the system.
-
- HF Recycling System
HF Recycling System
HFRS: HF Recycling System
Our system makes full use of our independently developed technologies to support recycling of the world's limited resources.
Equipment overview
- Directly recycles LCD panel etching fluid
- Provides high performance separation of the abrasive sludge trapped in the fluid by using a special filter unit for recycling
- Removes dissolved impurities in the fluid
- Maintains a stable etching grade by working in conjunction with an advanced concentration management system
Features
- Directly processes thick fluids without the need to dilute them
- Greatly reduces waste liquid because of the system's high recycling rate
- Removes impurities
- Maintains a stable etching grade by using an advanced concentration regulating system
- Can be used with regular or strong acids
Our systems are designed with recycling in mind, and reduce both the chemicals consumption and waste generation.
Equipment delivery experience
LCD panel related production equipment, etc.
Equipment specifications
- HF recycling rate can reach 80%
- Impurity removal rate can reach 90%
Specifications
Shown below is an example schematic diagram of the system.
- Ceramic etching system
Ceramic etching system
CES: Ceramic Etching System
Wet-etching device used for surface treatment and modification of the ceramic powder for solid-state battery material and cathode material.
Features
- Applicable to various chemical solutions such as acid and alkaline solutions.
- Space saving and compact design
- Clean & safety process design
- Easy-to-maintain design by giving consideration to handling of powder
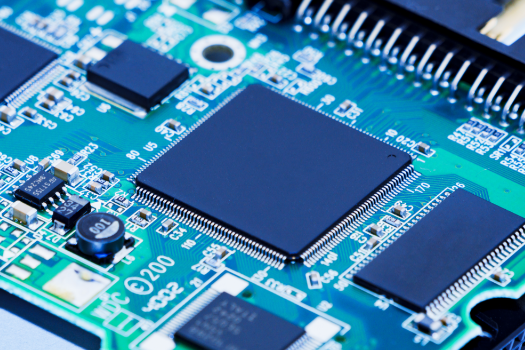
3Construction of Raw Materials and Component Plants Using a Variety of Solutions
We contribute to increase the competitive strength in the production of the different materials and components for semiconductors, batteries, and electronic devices through our engineering solutions cultivated in a wide range of areas that include chemistry, medicines, films and molded products. Our grasp of the changing conditions of the market is correct and timely so that we can find and solve problems early by sharing information with the many parties concerned, promptly address specification changes, and comply with safety measures, budgets, and delivery time. We provide total engineering from design to manufacturing and delivery.
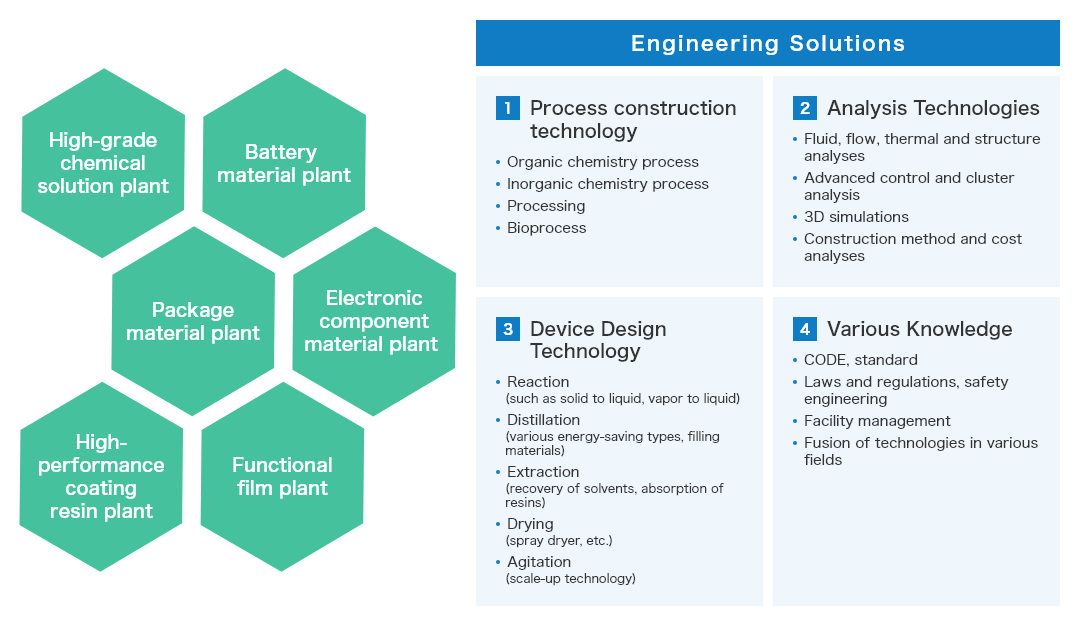
Related Technologies and Services
-
Film Casting Machine
Steel Belt Film Casting Machine Optimal for the Film Forming Process of the Dissolution Flow Casting Method
-
Solvent Recovery Technology (Recovery and Purification)
The organic solvents (such as NMP, DMF, and DMAc) used in manufacturing plants are recycled through a fully automatic facility using environment-friendly, energy-saving technology.