食品
よくあるご質問
食の安全
HACCP
HACCP導入は、今や食品会社にとって、企業の存在を左右するほどの大きな課題になっています。食品の危機管理対策やPL(製造物責任)法への対応の不備は、企業の死命を制することになり、これらの効果的な対策としてHACCPが有効とされています。
HACCP導入によるメリットの一例を示します。
- 1)製品(食品)の安全性が向上し、他社との競争力が強化される。
- 2)製造加工中および最終製品の廃棄といった無駄が減少する。
- 3)従来の経験や勘による衛生管理よりも、安定した安全な製品の製造が可能。
- 4)衛生管理の状態が記録されているため、製品の安全性が保証され、PL(製造物責任)法にも対応が可能。
食品工場におけるHACCP導入の目的を要約すると、「異物の混入」と「菌の増殖」の防止です。
その為に、下記のような手順や環境を科学的根拠に基づいて構築していくことなのです。
- 原材料の取り扱いは?
- 器具の管理は?
- 作業室・服装は?
- 作業手順は?
- 機械装置は?分析機器は?
等があります。
当社はHACCP導入におけるハード面のご提案はもちろん、ソフト面でもご提案できる関連会社(株式会社LSIメディエンス)を有しております。
HACCP導入=煩雑で費用と時間が掛かると思われがちですが、そうではありません。現状の管理方法を見直せば、より効率的・機能的に作業を進めることができ、工数が減ることもあるかと思います。
その際に、必要であれば設備投資を行うだけであり、設備投資が前提ではありません。
現状の課題に対して、さまざまな観点から対応を検討する必要があり、市場に出回っている機器・設備の情報や、同業他社の情報なども必要になります。当社は、数多くの食品工場の設計・建設の実績があり、お客さまのご要望にあった改善提案や機器・設備の選択が可能です。
CIP洗浄
さまざまなお客さまのニーズに対応するために、多品種の製品を生産していくことを要求される食品工場において、洗浄作業は必要ですが、厄介者でもあります。
多くの場合、「洗浄作業にかかる時間=生産できない時間」となり、生産性を阻害する要因にあげられることがあるからです。
CIP洗浄を導入することで、洗浄作業の効率化・短時間化の他にもさまざまなメリットがあります。
CIP洗浄導入によるメリットの一例を示します。
- 1)自動化を組み込めば、無人運転が可能→夜間洗浄で労働効率が上がり、人為ミスがなくなる。
- 2)洗浄性に再現性がある(作業者のレベルによる洗浄性の差異がない)。
- 3)系内がクローズド系に保たれる(人による汚染の可能性を除去)。
- 4)熱水や洗浄液との接触が少なくなり、作業者の安全性が向上する。
製品の種類、洗浄対象設備により洗浄条件は変わってきます。
また洗浄条件の決定には、さまざまな条件の値を仮定しつつ、実際に洗浄を行って、洗浄できているかどうかを検証していく作業(試運転期間での検証)が必要です。
新工場建設などの場合、洗浄方法を考慮した配管・配置計画が肝要です。一般的にCIP洗浄を考慮した設計の方が、送液や殺菌などのプロセス配管設計よりも高度で、経験の少ないエンジニアリング会社では、液たまりによるロスや洗浄不良によるトラブルなど、スムーズな立ち上げは難しいものです。
当社は、長年の食品工場建設に携わってきた経験と実績を基に、製品の液種や設備情報から、最適な初期値を設定しスムーズな立ち上げにご協力することができます。
お客さまの設備情報と要望事項を基に、従来からの洗浄手法を踏襲しつつ、効率的、安心・安全なCIP洗浄プロセスをご提案します。
必要なコストの算出につきましては、当社へお気軽にご相談ください。
誤投入防止
食品工場では、複数の原料を所定のレシピに基づいて調合し、調理することで、包装前の製品ができ上がります。
製品の多様化に伴い、製品サイクルが短く、レシピも増加することで、オペレーターの負担も大きくなり、「必要な原料の抜け」や「余分な原料の添加」といった誤投入が発生しやすくなっています。
食品工場では、所定のレシピに基づいて製品を製造しています。
その製造ロットサイズは非常に大きく、誤投入が起こると、そのロットは出荷することができなくなってしまい、製品ロス・機械ロスや回収コストが発生し、コスト増に跳ね返ります。
誤投入は食品工場において、生産性を下げる大きな要因のひとつとなっています。
誤投入は、オペレーターの操作ミス・計量ミス(ヒューマンエラー)によって起こります。誤投入を防止する為には、ヒューマンエラーを減らすことが必要になります。ヒューマンエラーを減らす為には下記のような方法が考えられます。
- 作業手順・オペレーター教育の見直し
- レイアウトや動線の見直し(製品ごとの原料管理スペース等)
- 誤投入防止システム導入でインターロックによる保護
当社では食品工場建設における経験と実績を基に、お客さまの立場でご提案をさせていただいています。
誤投入防止システムとは、製造現場での調合作業における誤投入のミスを回避する為に開発されたシステムです。システムの中には、原料管理の為のバーコード貼付や製造指図に沿った手順管理などさまざまな機能があります。詳しくは当社へご相談ください。
トレーサビリティ
食品会社においてトレーサビリティ(システム)を導入する場合、メリットとしては「リスク管理の強化」「製品に対する信頼度(或るいは安心感)の向上」などがあります。
例えば
リスク管理の強化の場合
間違って品質に問題のある製品(原料の一部に問題があった)が出荷されてしまった
↓
問題のあった原料を使用した製品はどのロットのものか?
今どこにあるのか?
↓
トレーサビリティ(システム)で迅速に特定することが可能
デメリットとしてはトレーサビリティ(システム)の構築は、食品会社にとって負担となることは否めません。しかし、社会的な要請は年々高まっており、政府主導でもその整備は求められています。
食品会社においてトレーサビリティ(システム)を導入する場合、まず原料等のデータベース化が必要になります。具体的な例として、原料の受け入れ単位ごとに受け入れ情報をデータベースに登録します。次にデータベースから受け入れ単位ごとにロット番号を含む情報が記録されたラベルを発行し、原料に貼付け保管・運用していくことになります。
手順や運用等のソフト面の変更だけでなく、データベースやラベルを印字するプリンター・読み取りのリーダーなどのハード面も必要になります。
ゾーニング・防虫・防鼠
食品工場におけるゾーニングのポイントはいろいろあると思いますが、簡潔にまとめると以下の項目になります。
- 一般区域(外部)と作業区域(工場内)を明確に分ける
- 作業区域を清浄・準清浄・一般区域などへの区分けと室圧の管理
- 人・物・製品の動線を明確に分ける
食品工場での防虫・防鼠対策は、①進入させない②持ち込まない③発生させないの3項目に基づき実施されています。
それぞれの項目での具体的な対策例としては、下記のようなものがあります。
- ①進入させない
- 扉の開閉ルールの徹底
- 防虫カーテン・防虫シートシャッターの採用
- 虫が寄ってきにくいライトへの変更
- ②持ち込まない
- 工場内部へ持ち込む包材などに付着した虫の除去(エアーブローの実施等)
- 木製パレット・ダンボール紙の清浄エリアへの持ち込み禁止
- 台車・靴底の洗浄
- ③発生させない
- 工場内外の清掃徹底
- 工場内のゴミの管理徹底
- 補虫器・殺菌剤の活用、UV灯の設置
フードディフェンス
従来の衛生基準は、性善説の考え方を前提としているのに対し、フードディフェンスは性悪説(毒物混入のように悪意をもって食品への混入を仕掛けることがある)を前提とするものです。
それらの攻撃から、食品や自分たちの安全を守るために必要な対策を行うことをフードディフェンスと言います。
悪意を持った攻撃(食品への異物混入など)から守ろうとする場合、自分たちの弱点(脆弱性)を知る必要があります。脆弱性を評価し、改善の為に必要な手段を講じることがフードディフェンスに繋がります。
フードディフェンスの具体的な一例を以下に示します。
- 1)施設や付属建築物への立ち入り制限の為に、敷地境界にセキュリティー対策を実施。
- 2)原材料を扱う屋外タンクヤードへの立ち入り制限と施錠の実施。
- 3)施設への入退場者管理の実施。
- 4)施設内の危害を与えられ易い場所への入場制限や監視カメラ・監視システムの導入。
- 5)洗剤や薬剤などの有害な物質を取り扱う場所への立ち入り制限や区画管理の実施。
当社は、一般的な手段や方法をご提案するのではなく、コストや運用を考慮し、お客さまに本当に必要とされているご提案をすることができます。
生産性向上
歩留まり
歩留まりとは、使用した資材量から想定される製品量に対する、実際に生産された製品量の割合です。
歩留まりを下げる要因としては、下記のようなものがあります。
- 人的要因
- 操作ミスによるオフスペック品の発生
- 機械的要因
- 設備やシステムの停止によるオフスペック品の発生
- 全設備的要因
- 設備内の残渣、配管長
- 運用的要因
- 回収した残渣の利用方法
歩留まりの向上を実現するためには、歩留まりを下げている原因や該当場所を分析するとともに製造ライン全体のバランスを考慮した上でハード面、ソフト面、オペレーター作業や運用方法等多岐面からの対策が必要となります。食品工場建設における多種多様な分野の経験を活かし、お客さまの抱える問題の解決をあらゆる面からサポートします。
生産性向上
工場では毎日多くの人・物が動いていますが、製品を作り出すまでの過程でそのパワーを100%有効に活用する事ができているでしょうか?生産効率が上がるということは、同じ量の製品をより少ない労力・資源で得ることとなり他社との競争力の強化という強みを得ると同時に、利益の向上にも繋がります。
生産性を下げる要因は多種多様です。
例えば・・・
- 労働時間
- 作業待ち時間、長い動線、生産時間の増加
- 資材
- 原料資材、包装資材、用役(蒸気・水・圧縮空気)等のロス
- 製品
- 生産ライン中の残渣、製品とならないオフスペック品
ラインを熟知した方が調査を行うのが最適ですが、生産担当の方が日々の生産を続けながら徹底的に調査を行うのは容易なことではありません。
当社は食品工場建設における永年の経験をもとに、さまざまな視点から調査を行いお客さまの工場に潜む無駄を見つけ出し、最適なご提案をします。
正しく計画して適切な設備投資をすれば、容易に生産性の改善を行うことはできますが、日々の生産の中でほんの少し手を加えるだけで改善することができる可能性もあります。運転ミス防止策、ラインバランスの最適化、ライン能力に適した生産計画のご提案、等々
まずは工場の現状を把握分析する事から始めてみませんか?
多品種少量生産
食品工場に限らず製造業全般において、消費者の要求に伴う製品の多様化と注文の短納期化によって、従来の少品種大量生産形態から多品種少量生産形態が必要とされています。
多品種少量生産には、詳細で迅速な生産計画の立案と管理が必要になります。これを達成するには、より高度な生産管理の情報システムを構築することがポイントとなります。
生産管理情報システムと名の付くシステムは数多くあります。多くのシステムはそれぞれに違った優位性を持っていますが、お客さまの運用に完全にマッチさせるには、基本パッケージ導入後にカスタマイズが必要となります。この基本パッケージ(システム)の選択を誤ると、後のカスタマイズが困難で膨大な作業となり、想定外のコストがかかることになります。当社は、長年の食品工場建設における実績と経験を基に、お客さまの工場に合った生産管理情報システムの選択を手助けすることができます。
多品種少量生産に適した生産管理情報システムの一例として、当社の「MECBLDR™食品・ファインケミカル向け製造管理システムパッケージ」があります。システムの詳細につきましては、お気軽に当社へご相談ください。
省人化・合理化・自動化の困った
人手作業のまま継続するか、自動機械を導入するか、多くのお客さまが抱える悩みの1つです。結論が出ないまま何年も経過してしまったという経験はないでしょうか?設備導入のためのコスト比較を行うことはもちろんですが、自動化によって更なるメリット、つまり「自動化=省人化」以外の効果を生み出すことができれば、設備投資は大きな価値のあるものとなります。
食品工場での作業は「人しかできない作業」も多くありますが、「機械ができる作業」や「機械の方が適している作業」も多々あります。下記のような「省人」以外のメリットを見出すことも、導入のポイントとなります。
- 品質向上
- 人が判断していた作業を計装機器に置き換えることで作業ミスが軽減。
人手作業を機械化、自動化することで製品の品質ばらつきの減少。
- 衛生化
- 人が介在しない作業にする事で衛生面の改善。
- 生産性向上
- 自動化を行うことでライン生産能力UP。
前処理作業の機械化、原料ラインを自動バルブと配管で構成、クッキングの無人化、CIPシステムによる自動洗浄化、包装ラインにロボット導入等、多種多様な方法が可能です。効率的な生産ラインを作り上げるためには、生産ラインの分析を行いポイントを押さえたライン構成とすることが必要となります。当社は、最適なライン構成となる機器の検討はもちろん、場合によっては用途に適した機器の共同開発も行います。
オペレーター教育
食品工場の生産には多くの人が関わっていますが、でき上がる製品には誰が担当しても変わらない均一な品質が必要とされます。機器やシステムの使用方法や安全な取り扱いを熟知した上での生産作業、トラブル時の対応等、オペレーターが習得しなければならない事柄は多岐にわたります。
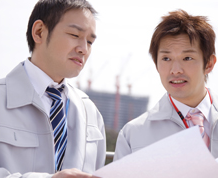
食品工場ではさまざまな機械が活用され、配管での移送が必要なケースも多々あります。生産をスムーズに行い、また多様なトラブルに対応するためには、機器単体の取り扱いに加え生産ライン全体を複合的に理解しておくことが不可欠です。また、機器の取り扱いについてもその工場の生産ラインに適した分かりやすい説明があるべきです。
生産ライン全体を理解するには、機器やラインを何のために、どの様に使うのかまた導入時の思想や経緯も知っておく事が有効です。当社はお客さまのパートナーとして設備立ち上げ時に必要なオペレーター教育をサポートすると共に、日々の運転や将来的な教育を考慮したオペレーションマニュアルをご提供します。
環境対策
環境対策
工場というものはモノづくりの現場であるため、オフィスや家庭よりも多くのエネルギーを使い、またさまざまな廃棄物が出てきます。 世界的にもエコが求められている今、工場の環境対策は大きな課題となっています。
騒音、防音、臭気、廃棄物、水処理、等々、環境対策にはさまざまなものがあります。例えばダクトの材質を布や段ボールで作るソックダクト・段ボールダクトを採用する事で、ダクト製作時や移送時のCO2排出量を減少させることが可能です。新工場建設でも既存改修でも、さまざまな目的と用途に合わせた最適なご提案をします。
既設屋根の耐荷重に余裕があれば太陽光パネルの設置が可能です。部分的に補強工事が必要になる場合もありますが、当社で構造を検討して設置の可否を判断します。また、屋根の耐荷重に余裕が少ない場合、軽量タイプの太陽光パネルを使うことも可能です。

例えば太陽光発電パネルを設置する場合、イニシャルコストはかかりますが電気代(ランニングコスト)の節減で投資額の回収も可能です。また、工場立地法の特定工場に該当する場合に、環境施設面積緩和の優遇も得られます。発電した電気を自家消費する場合、適用可能な補助金制度もあります。
節電・省エネ(CO2削減)
食品工場では、多くのエネルギーを使ってさまざまな商品を製造しています。しかし、このエネルギー消費には「無駄」や「ロス」が潜んでいることが少なくありません。
食品工場での節電・省エネとは、適切な状態での使用で、無駄・ロスを減らし、有効利用を図ることであり、ひいてはCO2削減に繋がっていくものと言えます。
食品工場において使用する主要なエネルギーには、照明・動力などの「電力」の他に「蒸気」「圧縮空気」「温水」「冷水」のように、電力や燃料を介してのものもあります。いずれもCO2排出に絡んでおり、それぞれに省エネに繋がる方法があります。
例えば、蒸気発生設備における省エネの場合、以下のようなことが考えられます。
- 配管や設備の断熱性を向上(保温の実施)により、放散熱量を抑える。
- 適正な圧力での使用でエンタルピーロスの節減。
- 排熱回収利用。
- コンデンセート(凝縮水)の回収による再利用。
当社は、食品工場建設における経験と実績を活用し、お客さまの運転状況を把握・分析することで、さまざまな節電・省エネの提案を行っています。
その他
改修・能力増強・スケールアップ
機能・用途変更(リニューアル)、工場増築、設備の能力増強、工場建て替え(スクラップ&ビルド)、工場改修等さまざまな方法があります。当社はリニューアルの目的や設備の用途、予算によってお客さまに最適な手法をご提案すると共にコンサルティングから計画・施工・稼動立上まで、一貫したエンジニアリングサービスでお客さまのイノベーションを強力にバックアップします。
食品工場のリニューアル(改修計画)やリノベーション(大規模改修計画)では、製造過程やスケジューリングにおけるさまざまな制約条件がネックとなり、計画がなかなか進まないというお話をよくお聞きします。この様な問題を解決するためには、工場建設技術やコストに加え「製造しながら施工する」ための計画から施工までの複雑なパズルを解くことのできる技術力と実行力、課題解決力が必要不可欠です。
効率的な改造を行うには製造ラインのボトルネックを把握する事が重要となります。当社はラインバランスのチェック(機器の余力過不足調査)を行うことでお客さまの生産ラインを最大限に活かす事ができる最適なプロセスをご提案します。
災害に強い・耐震診断の困った
世間的にも広く知られるようになった「建物の耐震」ですが、工場を建てる際に満たさなければならない法律があります。また、法律で決められているからという理由だけでなく、災害に対して備えるということはいざという時に従業員や見学者の人命を守り、企業を存続させる為の重要な社会的責任でもあるのです。
災害の対策といっても幅が広く、また専門知識も必要なため悩んでいるお客さまも多いことでしょう。当社はお客さまのご要望に対しBCP(business continuity plan)チームを工場へ派遣し、建物や設備の耐震診断を行い、ハード面から災害への対策についてリコメンドします。
既存工場に対しても、現状の建物の診断を行い耐震補強を施すことが可能です。また、建物だけではなく、機器設備の据付や既存配管の施工について、リコメンドと改善提案を行います。
見せる工場
食に求められるものはもう美味しい、安いだけではありません。確かな安全という土台のもとに、食品業界は成り立っています。安全・安心を実現している製造過程をお客さまである消費者に見せるということは製品を作っている人・機械を自らの目で見て、その安全性を確認していただくということです。
見学者通路とは生産現場の作業の様子を一般見学者が室外から確認するスペースです。食品工場では、見学者通路と生産ゾーンとは完全に区画され、見学者通路へのアクセスも従業員とは別のルートを確保する事が望ましいです。当社は工場全体の生産ラインを理解した上で、お客さまのニーズにお応えし、効果的な見せ方のご提案を行います。
天井の高いエリアの上部空間を利用して見学者通路を設置する、生産エリア各所に設置したカメラからの映像をモニターに映して説明が行える部屋を作る等、色々な方法があります。
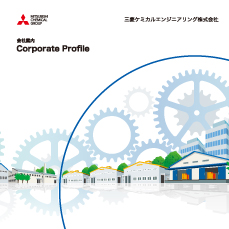
お問い合わせ
お気軽にお問い合わせください