固形製剤連続生産
連続生産システム構築ソリューション
従来の医薬品製造は各プロセスで生産機械を単独で設置するバッチ製造が行われていましたが、製造工程の効率化、高い品質保証等の観点から、
各製造プロセスを一連化する連続生産システムに注目が集まっており、すでに複数品目の固形製剤が連続生産によって製造されています。
当社は化学プラントにより長年培ってきた連続生産プロセスの構築技術と原薬、化粧品、食品製造などの豊富な実績によりお客さまにとって
最適な連続生産システムを構築します。
また、当社では2021年に「固形製剤の連続生産システム構築に向けた取り組み」により、田辺三菱製薬株式会社と第21回製剤機械技術学会仲井賞を受賞しました。
強み・特長
1処方に応じた装置選定と全体プロセス構築、運転方法やメンテナンスまでお客さま視点の最適な連続生産システムを構築します。
2PSE(Process System Engineering)& PAT (Process Analytical Technology)により、負荷低減、安定品質・安定供給の実現に貢献します。
3品質管理戦略構築をサポートする検査選別装置「iSorter™」により、オフ品を自動で選別できます。
4製造プロセスに合った品質管理戦略を立案し、最適な情報制御システムを構築します。
連続生産システム
連続生産システムでは、各プロセスの生産機械を一連化し、各プロセスの制御、搬送、品質管理を自動化することで、工場機能の1システム化を可能とします。
従来のバッチ式と比較し、連続生産方式は品質の安定化、生産性の向上、省スペース化など様々な導入メリットが得られます。
従来の医薬品製造(バッチ製造)
- 各プロセスで生産機械を、単独で設置=ワンルームワンマシン
- 各プロセス間は容器に入れて移動
- 各工程間で、混合均一性、含量、溶出性等を検査
各プロセスの生産機械を一連化(連続生産)
連続生産導入のメリット(例)
- 1.品質安定供給
- リアルタイムモニタリング 信頼性の高い製造が可能
- 2.柔軟な生産量に対応
- 稼働時間の変更により生産量を調整
需要の変動に柔軟に対応 - 3.製造設備省スペース化
- 設備の縮小、省スペース化
エネルギー消費量の低減
連続生産システム構築例
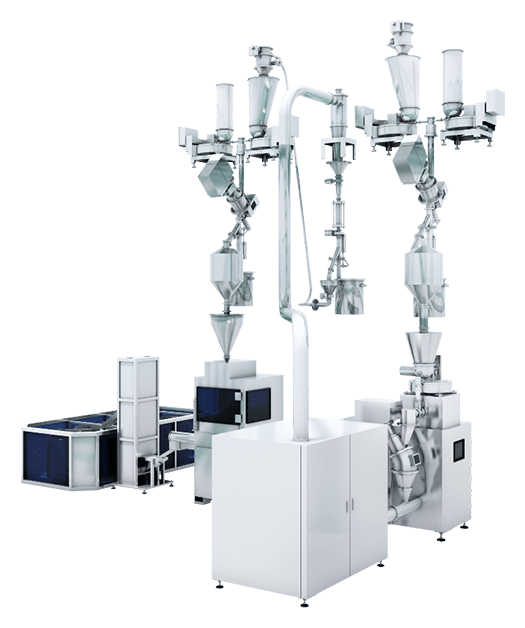
PSE(Process System Engineering)
プロセス構築は、処方・製法の理解、比較検討・装置選定、仕様検討・改善、システム構築とステップを踏むことにより、処方特性に適合する工程機器の柔軟な組み合わせを検討していきます。
構築する上で顕在化する設備課題を実験と工学設計、シミュレーションなどを駆使し改善に取り組みます。
粉体シミュレーション技術(例)
PAT (Process Analytical Technology)
PATとは、各工程において原材料や中間体の重要品質をリアルタイムで計測することで最終製品の品質を保証するための技術です。
連続生産時のリアルタイムモニタリングを実施するため、東京大学と共同でキャリブレーションミニマムソフトセンサーの開発に取り組み、従来法と比べ、キャリブレーションコストおよび負荷を大きく軽減することができます。また、NIR分光分析による検量の省力化に取り組みました。
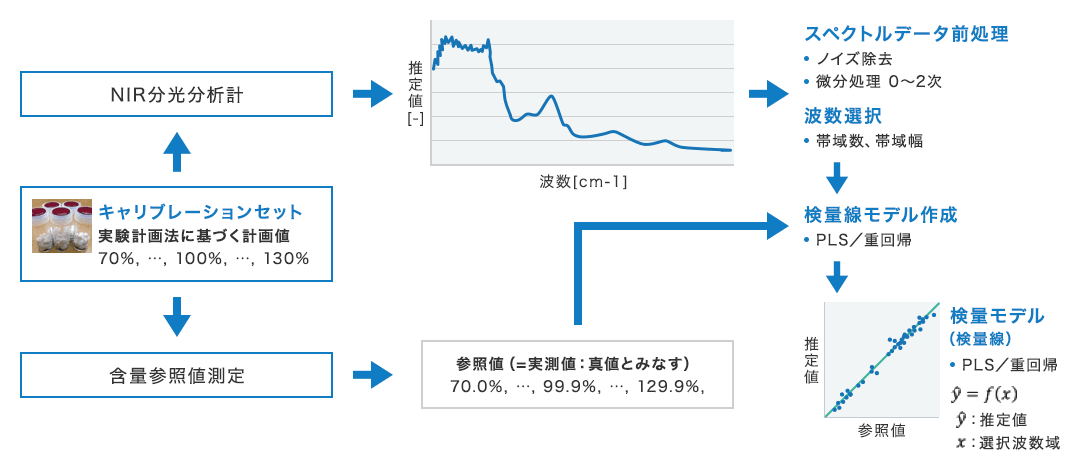
品質管理戦略構築をサポートする検査選別装置「iSorter™」
品質異常を検知し、基準に満たない品質オフ品を系外へ排出します。
1品質異常検知考え方
上流プロセス乱れを検知し、プロセスモデルを用いて下流側品質逸脱有無を判断
2実現するためのステップ
- 1.粉体残留確認・製品粉体の定量切り出し
- 2.粒径分布計、分光分析計等による品質測定
- 3.装置内ブロー洗浄

※特許取得中
MSPC(Multivariate Statistical Process Control)
多変量モニタリングシステムを構築し、原料から製品までの全工程の通常状態からの逸脱有無をモニタリングすることにより、
品質、生産性への影響の予兆を検知、さらには安定供給、ロス削減を実現します。
情報制御システム
連続生産において高い品質を維持するため、最善の機器を連結し、製造プロセスに合った品質管理戦略が必要です。
各プロセスの情報を一括管理し、お客さまの制御システムと連携し、最適なシステムを構築します。
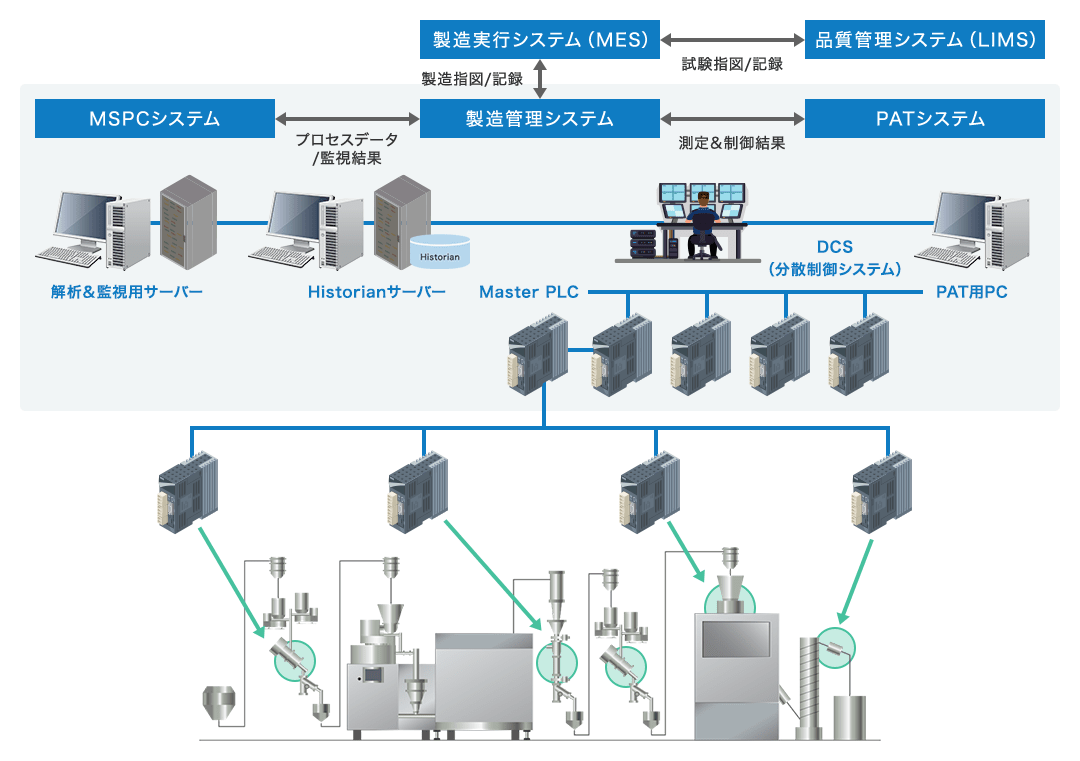
全体プロセス・システム構築
商業生産を行う上では、装置を選定するだけではなく装置間を配管などで連結し安定運転を行うための管理戦略、連続制御などの
全体プロセス・システム構築、また既存工場へ設置するためには用役、空調設備能力や建築構造面の評価、検討が必要となります。
さらにリスクベースアプローチにより必要な要求仕様をURS(User Requirement Specification)へ付加し、適切なクォリフィケーションを実施、
導入後は継続的な改善、最適化を図っていくことが重要です。
当社は総合エンジニアリング会社として一貫したサポートを行います。
関連分野
技術コラム
技術・サービス
お問い合わせ
お気軽にお問い合わせください